
Fall has finally arrived, sort of. It's still 80 degrees or thereabout each day, but the leaves are turning and it's beautiful around these parts.
Last week Amy was invited to demonstrate spinning yarn at Rickard's Mill in Beatrice, Alabama. Each year the town of Beatrice has a festival based around the making of cane syrup. On Thursday and Friday school children were bussed in from all over lower Alabama to learn about traditional crafts such as pottery making an soap making. Each day there were approximately 500 children. On Saturday the event was more like a typical festival. I brought my banjo, of course, and we Had a great time. Everyone we met was incredibly friendly and generous. I'm already looking forward to next year.

And as the year begins to wind down and the thanksgiving holiday approaches, I realize just how fortunate I am, and how much I have to be thankful for. I'm thankful to have friends and family, a roof over my head, Amy, three great cats, and a banjo to build. Seriously. It makes me very happy to piddle around in my granddad's shop. I am thankful to have such a meaningful and rewarding hobby.
As for the banjo, I decided to use the same wood for the cap on the pot as I used for the peghead overlay and fingerboard. I had planned on using the African Rosewood for the cap on the pot, but the ebony was so beautiful that I just couldn't resist using it on the pot cap also. Not very cost effective, but it will make a beautiful instrument.
I used 1/4" pieces of wood glued to the bottom of the pot to create the cap. To the left is a photo of the cap clamped to the pot.


Next I shaped the neck. To the left is a photo of the fingerboard scoop. I used a dremel tool with a router base to create the scoop.
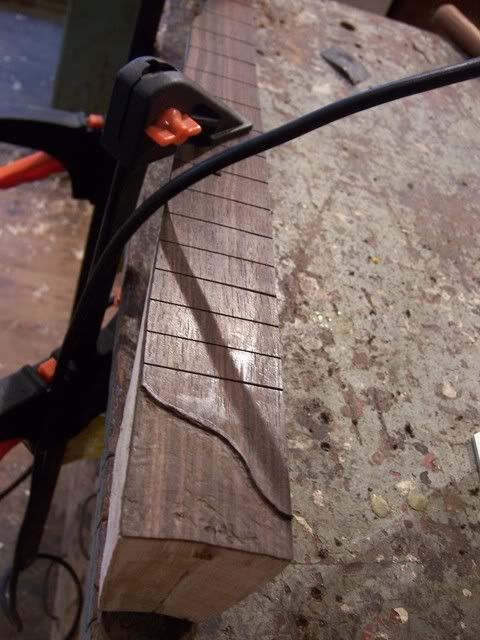
The scoop makes it possible, or at least more comfortable, to play the banjo clawhammer style. Most clawhammer and old time players play in this position because they believe that the tone is so much better there. Playing just above where where the pot and neck meet creates a nice mellow "plunk" that most old time players desire. The scoop on the fingerboard allows the thumb to grab onto the 5th string.


I also shaped the heel and performed the final shaping of the neck. I foresee a lot of sanding in my future.
To the left is a photo of the pot after it was grooved to accept the tonering, and that is the tonering resting against the pot. I use a simple brass tonering because it sounds the best for old-time music, at least to me, anyway.
And here is a photo of the tonering placed on the pot.
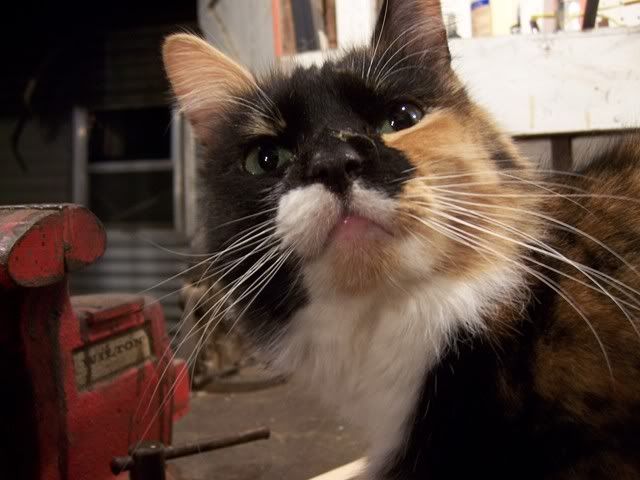


I also shaped the heel and performed the final shaping of the neck. I foresee a lot of sanding in my future.

And here is a photo of the tonering placed on the pot.
At this point, I think it would only be proper to introduce you to my trusty shop assistant., Fela. She's been a big help.
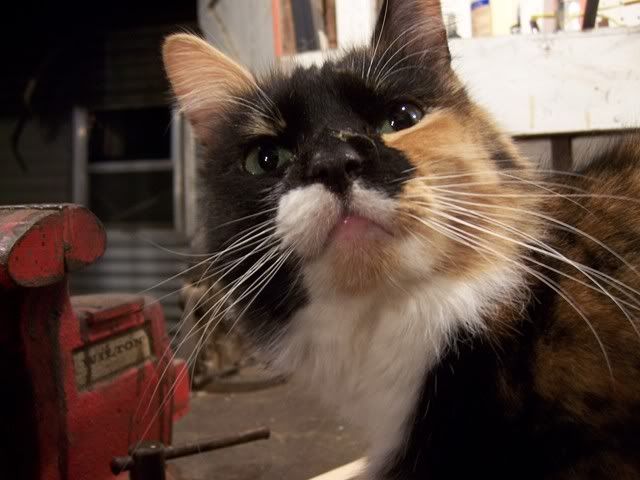



After I marked the pot for the brackets, I cut a hole to accept the dowel rod

I then drilled holes for the brackets. I placed them 1 1/2" apart.

And here are all of the parts that make up the pot. The upper left corner is the pot. beside the pot is the head. In the lower left is the brass tone ring, and beside that is the tension hoop.

Here the head is fitted over the tonering.
No comments:
Post a Comment