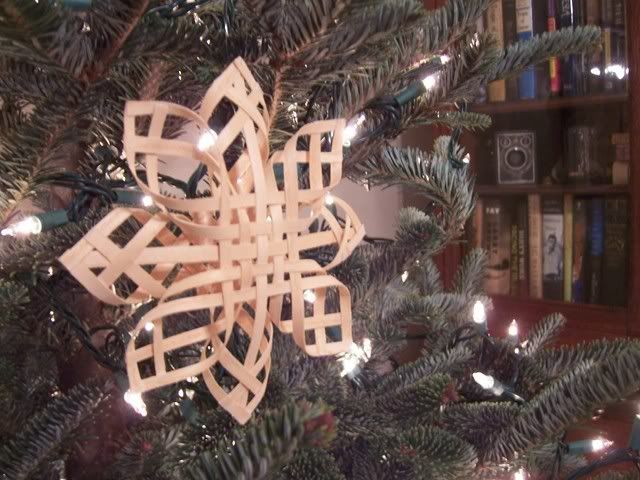
I hope everyone had a peaceful Christmas.
Many years ago my Mother started the tradition of getting the family together on Christmas eve for chili. Well, my small family has gotten smaller in the past few years, my mother and grandmother are no longer with us, but the family still gets together for chili on Christmas eve. This year was the first year that we gathered at my house, which was nice since it's the old home place. So, while it's sad that family members are gone, it is comforting that traditions remain. And how can family members really be gone when they live on in each of us?
Amy gave me a couple of luthier oriented books for Christmas. The title of this post, "you do the best you can, and very softly," is from the book, Hearts & Hands: Musical Instrument Makers in America. The quote is by Warren May of Berea, Ky, by the way.
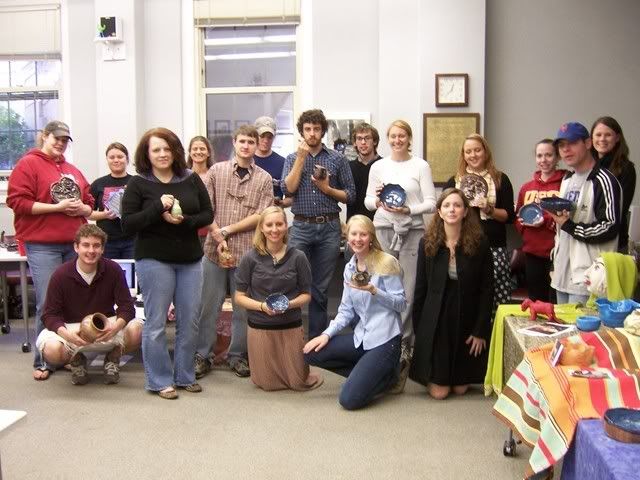
The class I was assistant teaching is over. Here's a photo from the last day of class. I don't think that you'll find a brighter group of folks anywhere. I'm sad that the class is over, it was certainly one of the most enjoyable experiences I've had. There's no profession that I admire more than teaching, and I'm fortunate to have had the opportunity to experience a little of what it is like to be one. I'm going to miss all the folks in the class.
My Friend Brian Kimerer just finished his first gourd banjo and documented the process. It's a beautiful and great sounding instrument. You can read about it at: http//www.thekimerers.com/brian/gourd/index.shtml
And now, on to the banjo:
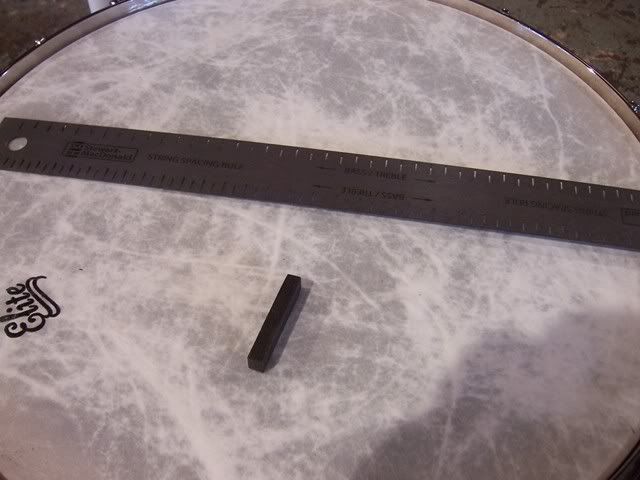
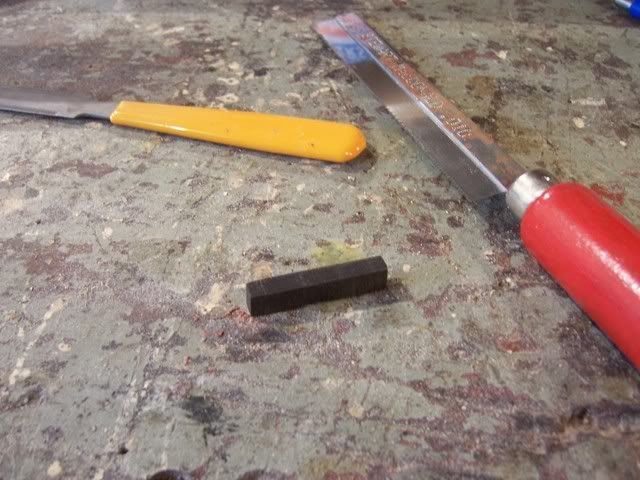
The photo to the left shows the tools that I used to notch the grooves in the nut. I used a small saw to make the initial cut, then a file to make the nut "v" shaped.
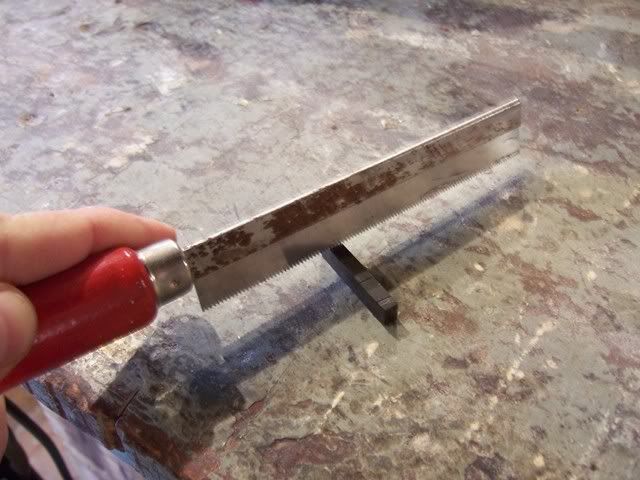
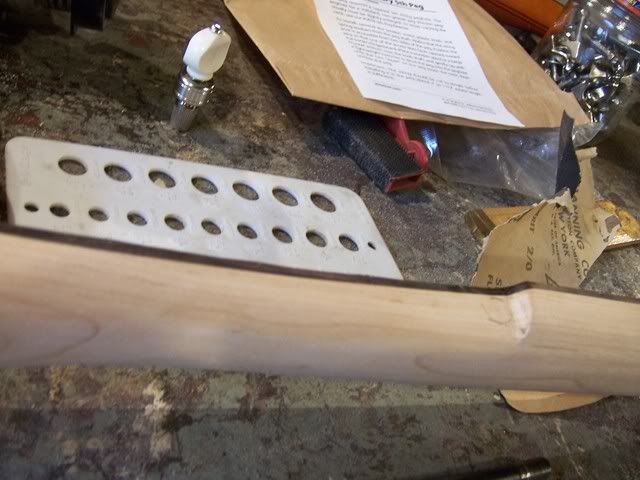
When the glue was completely dry I began to install the fifth string tuner.
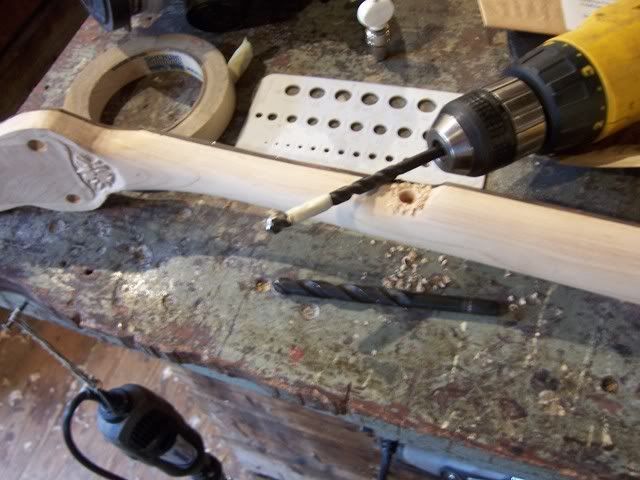
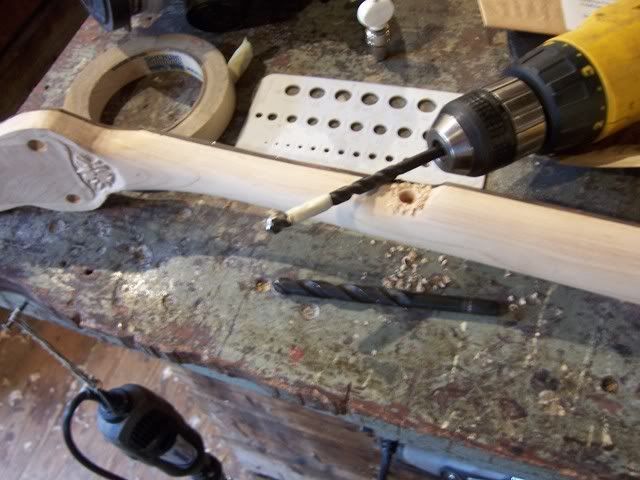
First I drilled a hole just shy of the correct diameter.

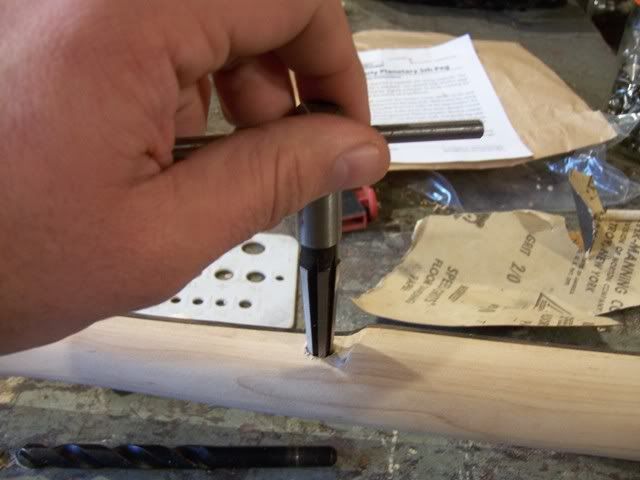
Next, I used the fifth string reamer to create the correct taper.
I removed the button off of the fifth string tuner and used a dowel rod with a hole drilled into the center to tap the fifth string tuner in place. By doing this, the shaft is protected from damage.
And here is the fifth string tuner in place.
Next I drilled the fretboard for the fifth string nut and glued the nut in place.
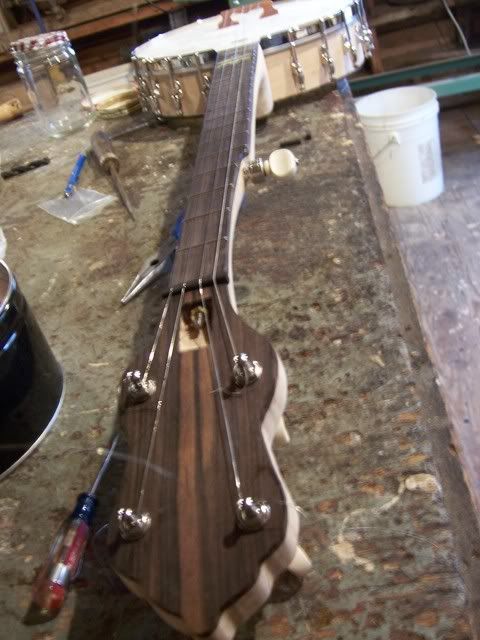
After the fifth string nut was in place I put strings on the banjo and made some slight adjustments. I forgot to take photos of the making of the bridge, but it was cut on the scrollsaw from rosewood. The rosewood gives the banjo a nice warm sound that's perfect for old-time music.

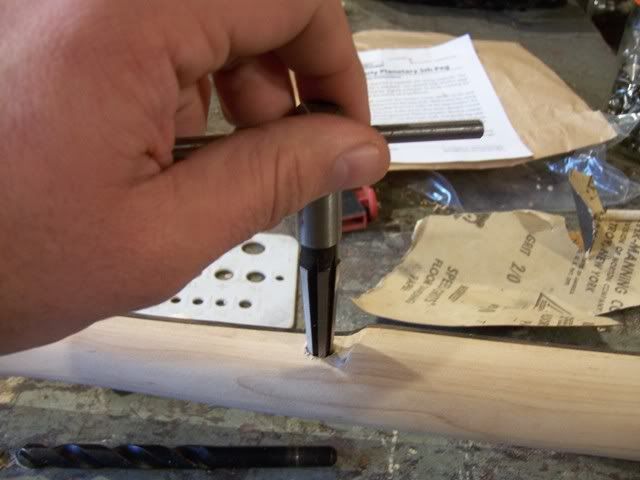
Next, I used the fifth string reamer to create the correct taper.
I removed the button off of the fifth string tuner and used a dowel rod with a hole drilled into the center to tap the fifth string tuner in place. By doing this, the shaft is protected from damage.
And here is the fifth string tuner in place.
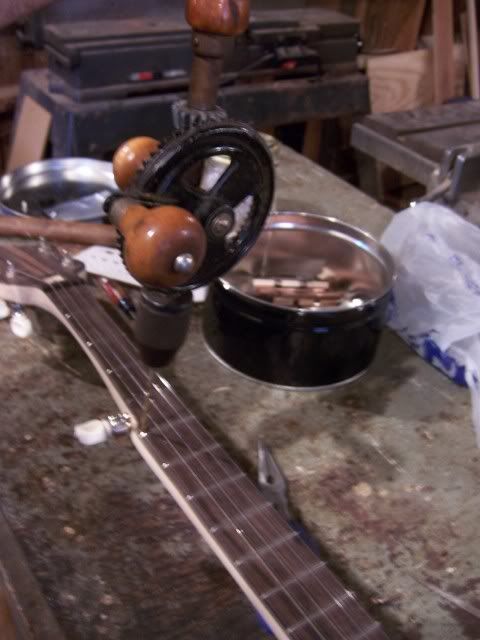
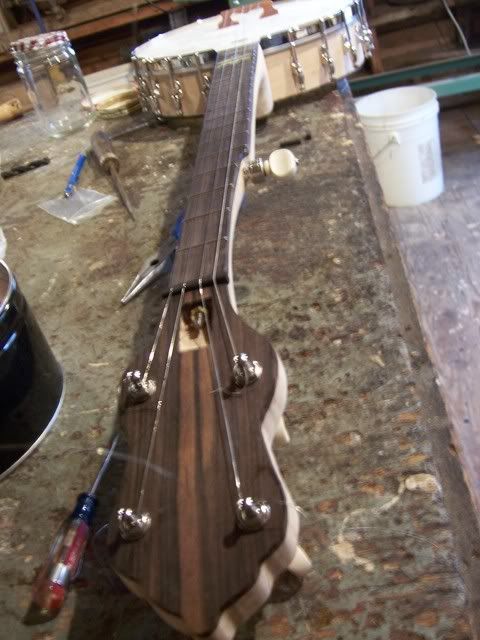
After the fifth string nut was in place I put strings on the banjo and made some slight adjustments. I forgot to take photos of the making of the bridge, but it was cut on the scrollsaw from rosewood. The rosewood gives the banjo a nice warm sound that's perfect for old-time music.
And with that, I think I'll call it a day.
No comments:
Post a Comment